印刷品覆膜后起泡是个让人头疼的问题,尤其是当你精心设计的作品在最后一步功亏一篑时。起泡不仅影响美观,还可能降低产品的耐用性。那么,为什么会出现这种情况?又该怎么解决呢?
覆膜起泡的主要原因
1. 纸张或材料湿度高
纸张在印刷前如果储存环境潮湿,或者印刷后未充分干燥就进行覆膜,水分会被薄膜封闭在里面。当温度变化时,水分蒸发形成气泡。
2. 胶粘剂与水分反应
覆膜用的胶粘剂(尤其是聚氨酯类)如果遇到空气中的水汽,会发生化学反应,产生二氧化碳气体。这些气体被困在薄膜和印刷品之间,就会形成气泡。
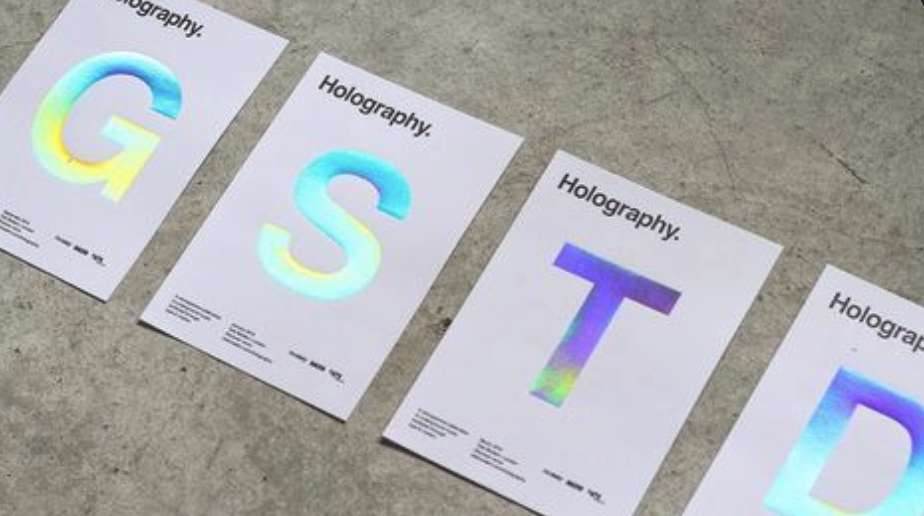
3. 油墨未干透或附着力差
如果印刷品上的油墨没有完全干燥,或者油墨与纸张的附着力不足,覆膜时胶水无法均匀渗透,导致局部粘合不牢,形成气泡。
4. 压辊老化或压力不足
覆膜机的压辊如果老化、变形或者压力调节不当,就无法将薄膜和印刷品紧密贴合,空气残留在中间,最终形成气泡。
5. 薄膜质量问题
劣质薄膜可能表面不平整,或者张力不均匀,导致覆膜时无法均匀贴合。
解决方法
1. 控制环境湿度
- 印刷前确保纸张存放在干燥环境中,避免受潮。
- 覆膜前检查印刷品是否完全干燥,必要时使用烘干设备辅助。
2. 选择合适的胶粘剂
- 使用低反应活性的胶水,减少与水汽的反应。
- 在湿度较高的环境下,可以适当调整胶水配方或增加固化剂比例。
3. 确保油墨完全干燥
- 印刷后留出足够时间让油墨自然干燥,避免急于覆膜。
- 对于UV油墨印刷品,确保固化彻底,避免残留未反应的成分影响覆膜效果。
4. 检查压辊状态
- 定期检查覆膜机的压辊,如果发现老化、变形或磨损,及时更换。
- 调整合适的压力,确保薄膜与印刷品充分贴合,避免空气残留。
5. 选用优质薄膜
- 选择表面平整、张力均匀的薄膜材料,避免因薄膜自身问题导致起泡。
- 覆膜前可以适当预热薄膜,提高其柔韧性,使其更容易贴合。
6. 覆膜后处理
- 如果已经出现小气泡,可以用细针轻轻扎破,再用压辊重新压实。
- 对于大面积起泡,可能需要重新覆膜,并检查前期的工艺问题。
预防比补救更重要
覆膜起泡的问题,很多时候是多个因素共同作用的结果。最好的办法是在生产过程中严格把控每个环节,而不是等到问题出现后再去补救。比如:
- 印刷后让产品自然干燥24小时再覆膜。
- 定期维护覆膜设备,确保压辊和加热系统正常工作。
- 在湿度较高的季节,适当调整生产工艺,比如降低覆膜速度,让胶水有更充分的时间贴合。
覆膜工艺看似简单,但细节决定成败。只要控制好材料、环境和设备,就能大幅减少起泡问题,让印刷品更加完美。
印刷品覆膜后起泡通常由纸张潮湿、胶粘剂反应、油墨未干、压辊压力不足或薄膜质量差导致。解决方法包括控制环境湿度、选用合适胶水、确保油墨干燥、检查压辊状态、使用优质薄膜,以及覆膜后及时处理气泡。预防关键在于严格把控印刷和覆膜工艺,如充分干燥、设备维护和调整生产参数,以减少起泡风险,保证成品质量。